Cathy Neal — July 1, 2014
Recent nursery production research conducted in the Northeast has far-reaching implications for the way trees and shrubs are grown, including plant health and quality, environmental impact and return on investment. In Part I of our presentation, we compare three types of production systems and their effects on tree growth and root morphology.
Click image to enlarge.
Tree production systems were evaluated in a three-year study in New England.
Demand for locally grown trees in the Northeast has increased over the past several years, as nursery production in this region has decreased and supplies have dwindled across the country. The Northeast imports much of its nursery stock from the mid-Atlantic and Midwestern states, but with rising freight costs and increased interest in buying local products, it may be time to re-examine the potential for more local nursery stock production. At the same time, environmental concerns have been raised concerning the removal of prime native soil inherent in some production practices.
To answer some of the lingering questions about which production methods are most efficient and produce the best quality plants—and to help nursery producers prepare for a future that may include higher energy costs and more regulatory restrictions—Dr. Daniel Lass and I conducted a three-year study comparing tree production systems for Northeastern nurseries. Dr. Lass is professor and chair of the Department of Resource Economics at the University of Massachusetts-Amherst; his part of the research concentrated on comparing the economic efficiencies of each system, and his results will be presented in an upcoming issue. In this report, we’ll take a look at how each of three growing systems affects the quality of nursery-grown trees.
Study basics
In order to help determine the comparative benefits of tree growing methods, we selected three commonly employed production systems for this study: field-grown or balled-and-burlapped (B&B); pot-in-pot (PiP); and in-ground fabric containers (IGFC). B&B has historically been the prevalent practice in Northeastern nurseries, and PiP has been more commonly used in the South but has spread rapidly northward and westward. The more recent system using a new generation of in-ground fabric containers rounded out the study. Fabric containers were obtained from two sources: Rootmaker (http://www.rootmaker.com) and High Caliper Growing Systems (http://www.treebag.com), but were not compared against each other, as different tree species were grown in each type. Two popular species – swamp white oak (Quercus bicolor) and multistemmed river birch (Betula nigra) – were grown and evaluated at two locations: Amherst Nursery in Amherst, Massachusetts, and the University of New Hampshire AES Horticultural Research Farm in Durham. A third species – ‘Prairifire’ crabapple (Malus × ‘Prairifire’) – also was planted, but harvest data were obtained only from the UNH trial. Bare-root stock was sourced from the same kind of large nursery stock suppliers used by commercial growers.
Click image to enlarge.
Three growing systems were evaluated: field-grown (B&B), container (pot-in-pot) and fabric container.
We chose river birch because it is a very popular la ndscape tree in the Northeast, especially the clump forms. Likewise, crabapples are always in high demand and are well-suited for local production.
We also used swamp white oak, a large-growing shade tree native, of course, to wetter areas, but it also adaptable to upland conditions. Because of the impending threats of Asian longhorned beetle, emerald ash borer and other new pests, we were trying to find something that wouldn’t be susceptible, was native and was readily available when we needed it. These tree species also have very different root characteristics; river birch is a really fast growing, almost weedy tree with a very aggressive root system. Swamp white oak has an interesting, bilayered root system that is very sparse compared to river birch.
Click image to enlarge.
Very different results were obtained when river birch were grown in three different production systems. B&B roots have some large diameter roots near the top, with a strong horizontal growth pattern. The rootballs on container- or fabric bag grown trees are much more compact and dense, with many more small diameter roots packed into the rootballs.
Seventy-five to 100 trees per species were planted at each location beginning in April 2010, in randomized complete block experimental designs with five trees per treatment in each block. Trees were spaced at 6 feet within the rows and 9 to 11 feet between rows, depending on the nursery. The birches were planted as 3-foot whips (in clumps), and the oaks and crabapples were 5-foot, lightly branched stock. PiP liner pots were trade 15-gallons (50 liter) filled with a commercial nursery mix (80:20:10 pine bark:peat:sand), and the 16-inch fabric containers were backfilled with equivalent volumes of field soil.
All plants received one application of preemergent herbicide and one application of slow-release fertilizer per year. Separate low-volume irrigation zones allowed the systems to be watered as needed, daily for the PiP trees in the heat of summer and an average of two to three times a week for the field and IGFC trees. The swamp white oaks were grown for three seasons, and the faster-growing river birches and crabapples were grown for two seasons. Our goal was to achieve 2-inch caliper minimum trees—typical for commercial sales—before digging to analyze the root growth.
Weights and measures
At the end of the growing season, once trees had dropped their leaves and gone dormant, we dug them, measured and weighed them, and began evaluating the root systems. Tree height and trunk caliper were no different between production systems except for river birch, where FC and PiP trees were smaller than field-grown trees.
Striving to maintain a real-world approach, we contracted with a commercial nursery to harvest the B&B plants with a tree spade. The IGFC trees, as well as the PiPs, were relatively easy to remove with hand labor. Once the trees were harvested and the total product weights recorded, we then cut the tops off at soil level, so we ended up with a root ball from each tree that would be typical of a harvested product. It was soon obvious that root defects (large-diameter circling, descending and bent roots that can become limiting to tree survival and growth) were minimal in field trees and most severe in PiP trees. Roots of IGFC trees were modified by the fabric bags, often forming root nodules or masses against the sides and bottom of the bags rather than circling along the interface.
We cleaned the root balls, both with water and by using an air spade, to remove as much of the soil as possible. The root balls of the B&B and IGFC plants were easily cleaned with the air spade; the PiP plants, however, were grown in a peat-pine bark substrate and the roots were so dense that the air spade didn’t do much more than knock off the outer inch of substrate. Considerably more time and effort were expended to clean the PiP roots, scrupulously cutting them apart and washing each and every root, a process that took dozens of hours per tree.We cut apart the clean, dry rootballs from the other systems as well, and separated individual roots into size classes by diameter. We eventually consolidated them into three main size classes: fine roots (less than .125-inch diameter), medium-diameter roots (.125- to .75-inch diameter) and large, structural roots (over .75-inch diameter). Total root biomass was not significantly different between production methods for oaks or crabapples, but there were very interesting differences in the proportion of the roots in each of those size classes.
With the PiPs, we ended up with most of the root mass in the fine root class as compared to the B&B product. With B&B, most of the fine roots are left in the field, so what remains are roots that are closer to the trunk that are larger in diameter. There were relatively few medium diameter roots in either PiP or B&B, but more in the fabric containers. So, we had more fine roots in IGFC than we did with the B&B product but not as many as in the PiP; there were fewer large diameter roots than in the B&B product but more than with the PiP. This makes sense, but because this kind of research is so labor intensive, we haven’t seen similar results reported.
It’s a common industry assumption that with field-grown, B&B trees, 90 percent of the roots are left in the field when they’re harvested. But, that assumption is based only on total root length, not mass. By digging with a tree spade, you’re leaving a lot of the small-diameter roots in the field. However, if you’re considering root mass, which we measured as dry weight, there was no difference between the total amount of roots contained within a B&B product, a PiP product or a field-grown, fabric container product.
Unlike crabapple or oak, total root mass for river birch was significantly greater in PiP than field or fabric containers. And, very interestingly, the root-shoot ratio was altered. The PiP river birch trees actually were putting more resources into roots as a proportion of the total plant biomass than in either of the other two systems, explaining why the top growth was somewhat smaller on the PiP trees.
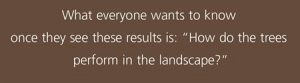
Which system?
It’s only when you have them side by side, or when you’re performing these expensive tree deconstructions, that you can see the small differences in trees grown from different production methods. And that’s kind of what this type of research is all about – to see things that people may not see when they go to a broker or a wholesale yard or a nursery. They don’t have the advantage of seeing trees that were grown from the same stock at the same time, using different systems. Even a grower would not normally have side-by-side comparisons with all the other factors controlled: water, nutrition, same planting stock, same production time, weather conditions, and so on.
Based on this research, I’d say that field growing B&B stock is still the gold standard for Northeastern nurseries to produce high quality trees. But, I’m not sure that’s going to be viable in the long run because of the environmental concerns about soil removal, and because of the economics of harvesting and shipping such large, heavy products. The field-grown fabric container provides a good alternative to B&B, from my standpoint.
Fabric container trees are lightweight because during harvest, only about half as much soil is removed as compared to a B&B plant. Consumer and landscape purchaser acceptance is still a challenge, however. The fabric container is not as stable as a plastic container when it’s on display in the sales yard, and it should be heeled in or repackaged somehow to conserve water in the rootball. And of course, the consumer needs to be educated on how to remove the fabric container when planting the tree.
Click image to enlarge.
You can watch footage of work at the test sites and listen to Dr. Neal and Dr. Lass discuss their research at http://www.youtube.com/watch?v=Umc_tQBsDd8 and http://www.youtube.com/watch?v=h6ZrnQdOAL4&feature=mfu_in_order&list=UL
The pot-in-pot system, like above-ground plastic containers, has some quality limitations in terms of how it impacts the root architecture of the tree, but it has some real advantages, as well. You can harvest the trees anytime, they’re lightweight and easy for the customer to move and handle. For a garden center, it appears to be a more realistic product than either a B&B tree or a fabric container tree. Growers should be very careful to avoid keeping trees in containers too long, however, because large circling roots are very hard to correct and can limit the long-term health of the tree.
Transplant performance
What everyone wants to know once they see these results is: “How do the trees perform in the landscape?”
Twelve harvested river birch from each of the three production systems were set in above-ground rows heeled in with wood chips for two months, then transplanted in June 2012. Half of the trees from each treatment were root pruned to remove any visible defects, and 2-inch-thick root mats were removed from PiP trees. In November 2013, trees were air-spaded to expose roots in a 3-foot-wide by 1-foot-deep trench the length of the tree row. We counted the number of roots at 3-foot, 5-foot and 7-foot transects and measured the extension of the longest roots in each direction.
Click image to enlarge.
Once we used air and water to wash the soil off, we cut up all the roots and sorted them into piles according to size (diameter). Here you see a deconstructed rootball with a large mass of storage or structural roots (66 percent by weight), a lot of woody, medium-sized roots (20 percent by weight), and not so many fine or feeder roots (only 14 percent by weight). Note the total dry root weight is 3.5 pounds.
All trees were able to establish new roots, with a mean north-south spread of 11.7 feet for PiP, 12.1 feet for IGFC and 13.3 feet for B&B trees, which corresponded with total stem caliper increases of 2.0, 2.7 and 3.7 inches, respectively. These differences were correlated with initial tree size (B&B trees were largest and PiP smallest at transplanting). The strong radial distribution of structural roots observed in field-grown trees is purported to be the best structure for long-term tree health.
Circling roots in unpruned PiP rootballs were still prominent and enlarged, which would potentially restrict growth in future years; however, they did not prevent successful extension of new roots into the surrounding soil during landscape establishment. Root pruning to remove defects in PiP trees at transplanting was successful, and no additional defects were observed at the termination of this experiment. The IGFC trees generally had good root structure but some new roots grew inward or tangentially to the original rootball.
Click image to enlarge.
Quite a different root size distribution can be seen when breaking down the PiP-grown rootball by size of roots. There is much less mass in storage roots (38 percent compared to 66 percent) than with B&B, with many more fine roots. But the total is essentially the same: 3.6 pounds of roots.
Today’s grower faces so many challenges: Environmental, economic and marketing concerns are just a few. In Part II of our report, we’ll address the comparative economies of the three growing systems covered here.
Special thanks to the USDA’s National Institute of Food and Agriculture, which provided the grant funding to support this research. The New Hampshire Agricultural Experiment Station provided additional support.
Click image to enlarge.
Breaking down the roots from a fabric container, an intermediate situation becomes evident: relatively few fine roots, more medium roots and an intermediate amount of storage roots, with a total root weight slightly less than that observed with B&B or PiP-grown trees.
Thanks also to John Kinchla, owner of Amherst Nursery, for his cooperation and assistance in this study, and to Amy Papineau for her technical assistance and dedication to root cleaning.
Cathy Neal, Ph.D., is Extension Professor in the Dept. of Biological Sciences, and nursery and landscape horticulture specialist for University of New Hampshire Cooperative Extension She can be reached at [email protected]. Daniel Lass is Professor and Chair of the Department of Resource Economics at the University of Massachusetts, Amherst. He can be reached at [email protected].